Parts made to the correct specification is a minimum expectation for customers. We have robust quality systems and checks in place to make sure we meet the standards customers expect. All operators are responsible for the quality of their own work, backed up by quality control inspections for key features.
We take great care in how we pack our products to protect against handling and transport damage – particularly for export. We discuss packaging at an early stagein the project to ensure we meet all the packaging requirements of the customer. Often, to save on packaging waste, we are able to specify a pack that the customer can reuse in their processing or final pack.
Key strengths:
- ISO 9001: 2015 - audited by BSI
- gauge calibration and control
- poka yoke mistake proofing gauge and process control built in at design stage
- first-off initial sample inspection reports are standard procedure at every set-up
- shopfloor and QC statistical process control
- full dimensional first article packs for new jobs
- PPAP (production part approval process)
- capability studies
- process control plans
- gauge repeatability and reproducibility (R and R) control
-
metrology
- CMM
- Shadowgraphs
- Tensile testing
- surface finish measurement
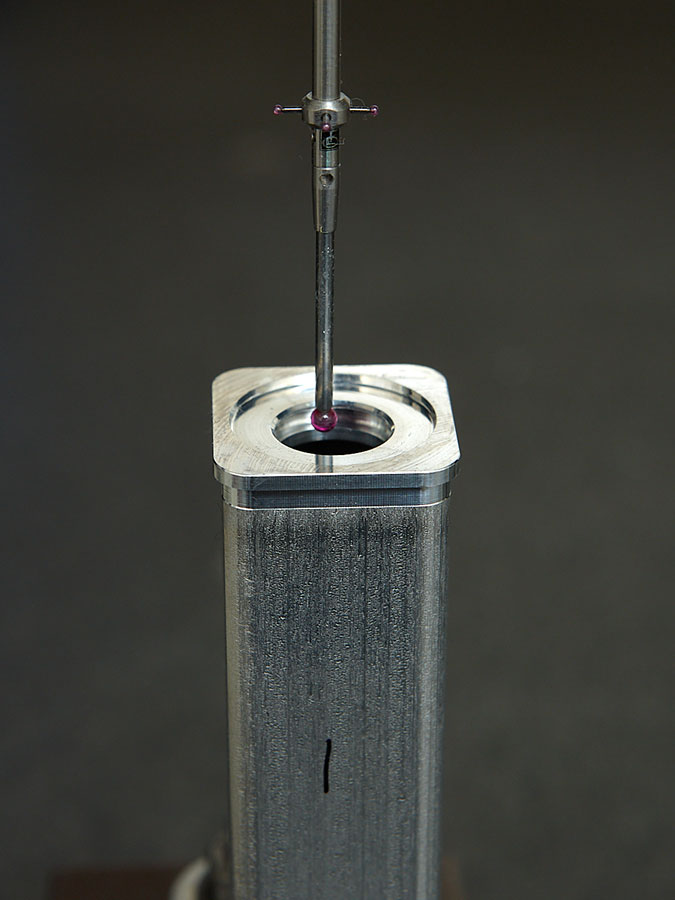
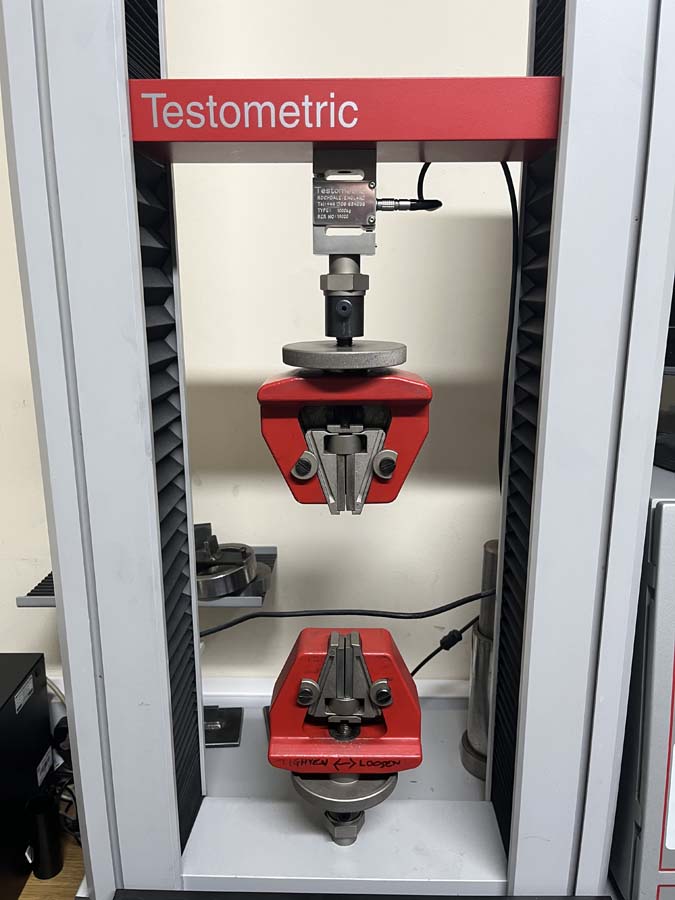
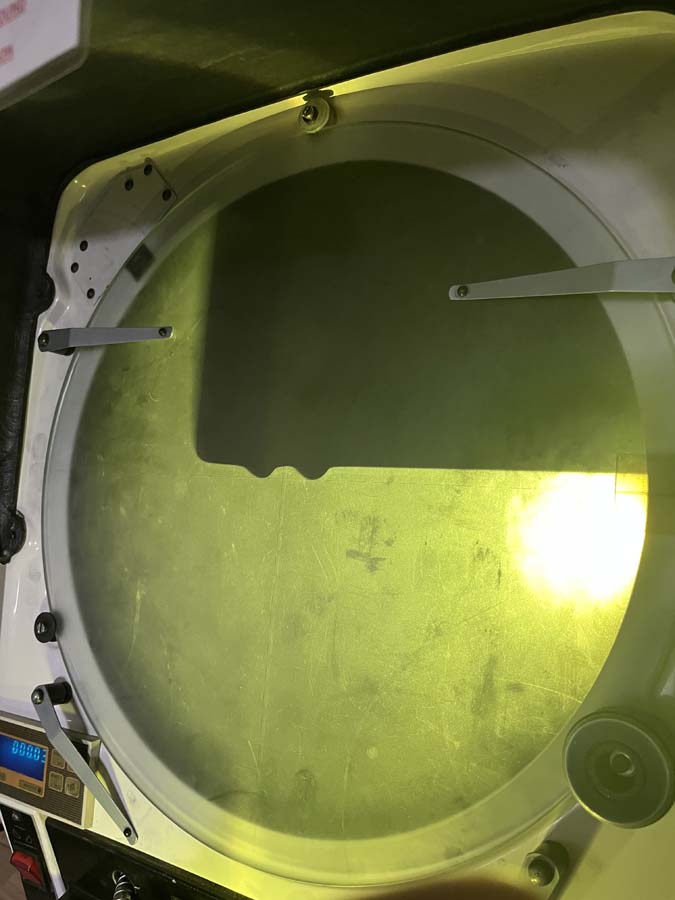