We have a New Product Development (NPD) team that develop parts from initial concept to initial samples and then into full production.
Whether it be a brand new part, or an existing part being converted for impact extrusion, we work with our customers to give the best, most economic and viable solutions. The earlier in the design process we can be involved, the better. We can often enhance designs to include features within the extrusion that might otherwise need extra machining or even separate parts. Often we are presented with a drawing designed for different processes such as casting or machining from solid – this is where the near net shape benefit of impact extrusion can really make a difference to the economics of manufacture.
A typical development process would consist of:
- receipt of enquiry
- initial discussion of application and ideas around design (if design not already fixed)
- receipt of customer drawing or creation by us of component drawing
- initial discussion of key features and tolerances
- design recommendations to suit extrusion / add benefits
- quote for volume production, tooling and initial samples
- tooling and process design
- production of initial samples and first article inspection measurements and reports subject to requirement
- FMEA (failure mode effect analysis) subject to requirement
- review and further development as required
- first production run
- hand-over to the production team for future manufacture
This collaborative approach can bring significant benefits. Examples of notable successes are:
- incorporating upstand into an extrusion that was previously a separate part that the customer could otherwise miss out in manufacture
- pressing a rectangular nose cone out of copper that was previously machined from a solid round bar
- incorporating electronic shielding collar into extrusion
- one-piece cans to replace fabricated cans with side seams and seamed on ends
- diameter changes off extrusion to reduce number of extra operations / machining
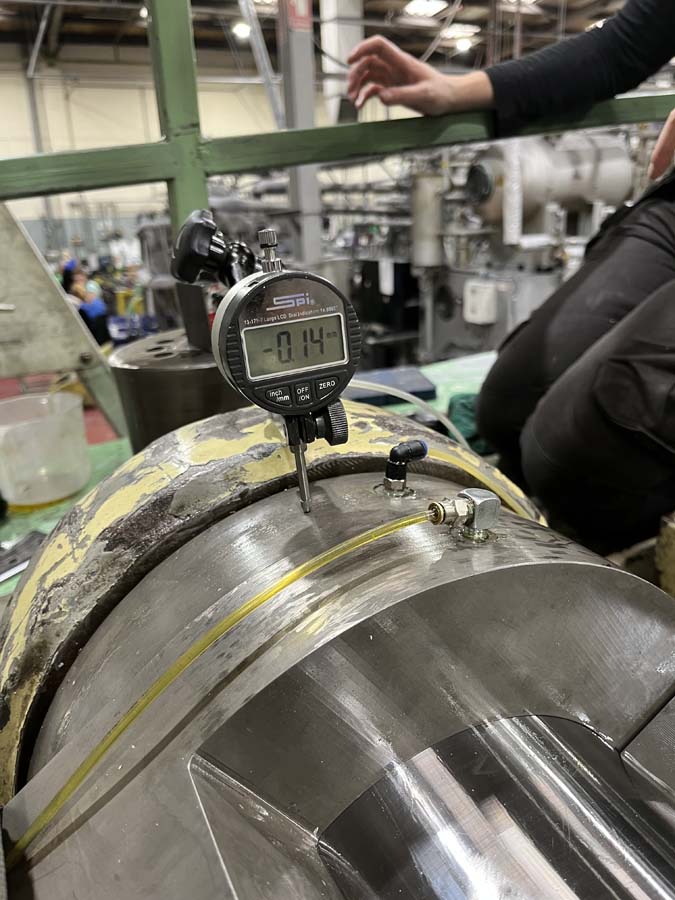
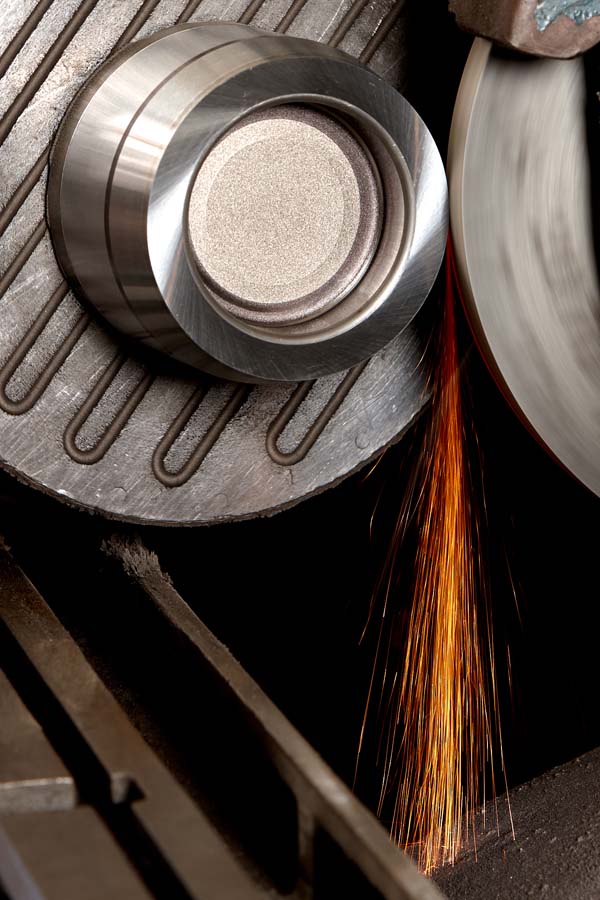